Tales of boatbuilding, family, paddling, music, camping, football, snowshoeing, kids, cycling, and whatever else suits my fancy.
Thursday, December 20, 2007
Merry Christmas!
I've been very busy at work lately, getting home late and sometimes coming back after the kids are asleep. I've also been out in the shop before work & after everyone's asleep trying to finish the Christmas presents I am building for the girls (shhhh... don't tell them but I'm building a doll cradle for each of them). Lots of trial & error, plus as usual everything is taking about ten times longer than I figured it would. Last night they were glued & screwed together, and the holes filled with plugs cut using a Veritas plug cutter. After trimming the plugs used to fill the screw holes early this morning and some final staining I should be varnishing them tonight with any luck. Then tomorrow I can varnish again, and maybe again of needed. Then hopefully the varnish will mostly cure by the time we leave for Christmas.
Monday, November 26, 2007
Monday, November 19, 2007
Tuesday, November 13, 2007
What Next?
I think a small kid's kayak will be first - the Yost Sea Flea perhaps. (Here is a recently completed example.) Boatbuilder Donald Taylor visited me while in town a few months ago on a trip from his home in New Brunswick. In addition to showing me photos of his guillemot, he also showed me photos of the Sea Flea he built for his 6-year old daughter. We talked a lot about the building process for the Sea Flea and my wife too thinks this would be a good thing to build for our daughters. I mentioned the idea to our older daughter and she is quite excited by the prospect of having her own kayak that she could help me build. In fact, I recently found this drawing taped to the wall: (excuse the b&w scan)
So I guess that's been decided and it's just a matter of when, how, and what colour.
Then maybe another kayak, for me this time. I think it would be a stitch & glue in order to get something on the water a little quicker. Something like the Point Bennett 18 maybe. A folding skin-on-frame kayak like one of those designed by Tom Yost has a certain amount of appeal too.
Or maybe my next build should be a fast tandem tripping canoe. Like the Green Valley Winisk (I already have the forms for a Kipawa, but I think something larger would fit the family better) or the Bear Mountain Freedom 17-9.
Or, maybe I'll go big with the 18'6" E. M. White Guide canoe from Gilpatrick's book or Green Valley's Quetico. Or maybe I'll go smaller with a solo canoe. The stitch & glue Osprey II from Green Valley appeals to me because of the quicker build of a S&G boat, but I think it's too small for me (plus I can't seem to find it on their web site any more?). The 16-2 Freedom Solo seems pretty much perfect though for me in that category. Or maybe I'll build a small tandem, something I can paddle solo but can have my girls along while they are still small, or which they could tandem paddle when they are older.
However, before I build anything else I want to improve the wiring in the garage/shop & the heating as well. Hmm, maybe I should go clean up the garage first.
Thursday, September 20, 2007
Guy Clark, Boats To Build
I'm gonna build me a boat
With these two hands
It'll be a fair curve
From a noble plan
Let the chips fall where they will
Cause I've got boats to build
Wednesday, August 29, 2007
Nathan Rogers House Concert
Sorry, the player has now been disabled since it slows things down and can be somewhat annoying when it comes on too loud. Click the image to follow a link that will let you hear more of Nathan's great music.
Nathan Rogers is a folk rock musician out of Winnipeg. Recognise the voice? Nathan is son of Stan Rogers, nephew of Garnet Rogers.
Speaking of cool, if the embedded player, courtesy of CBC Radio 3, actually works, now that would be cool. (That seems like a few too many comma's for one sentence, no?) Let me know if it works for you, & if you hate the player or like it.
Edited to remove the embedded player on October 3, '07.
Friday, August 24, 2007
Carving on Deck
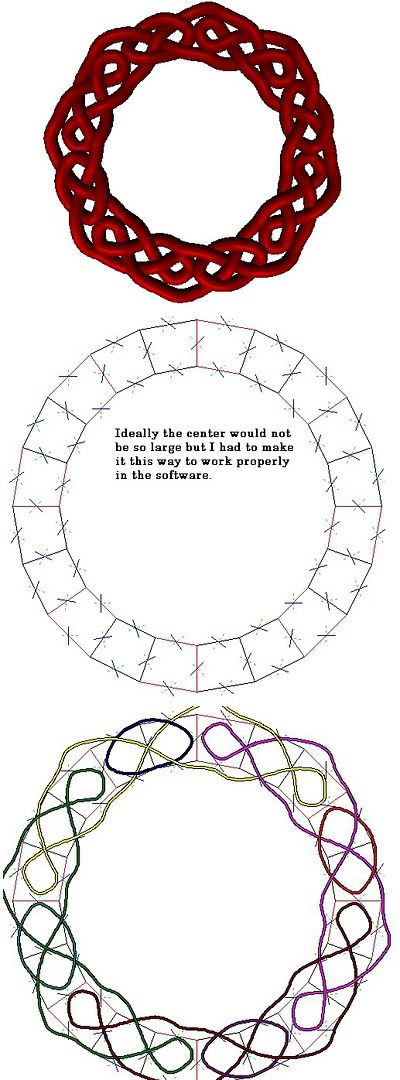
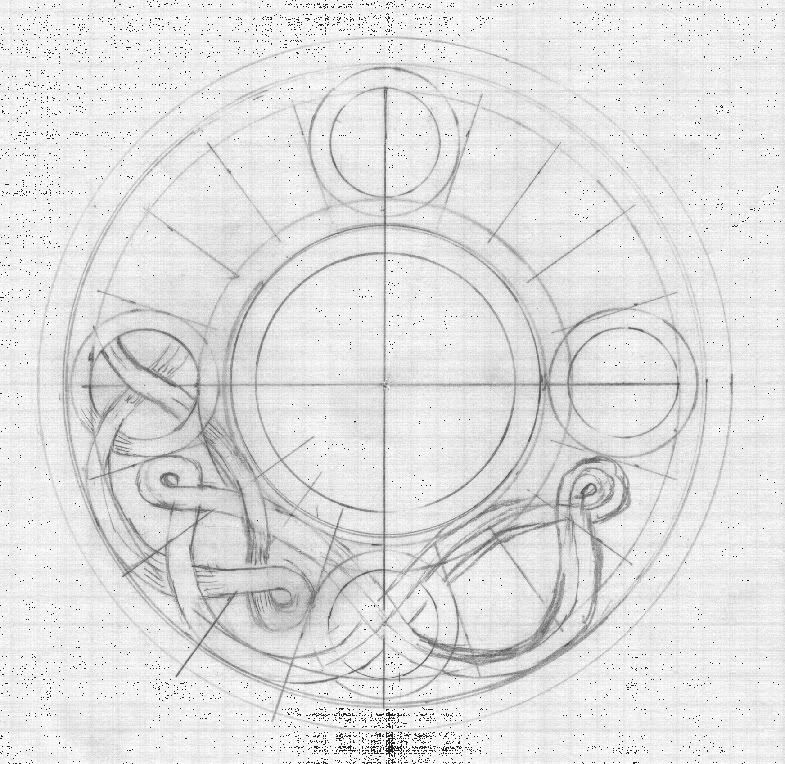
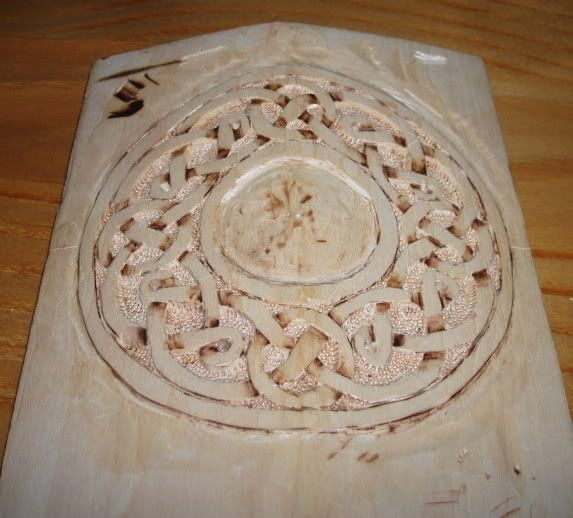
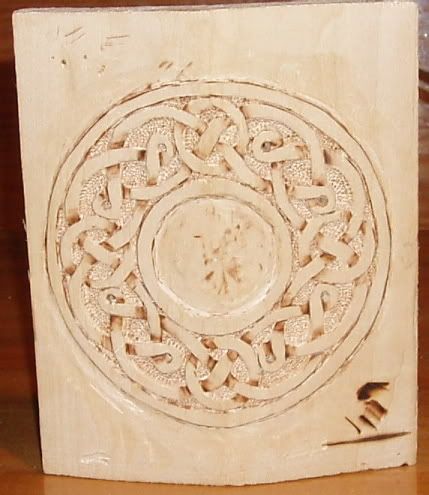
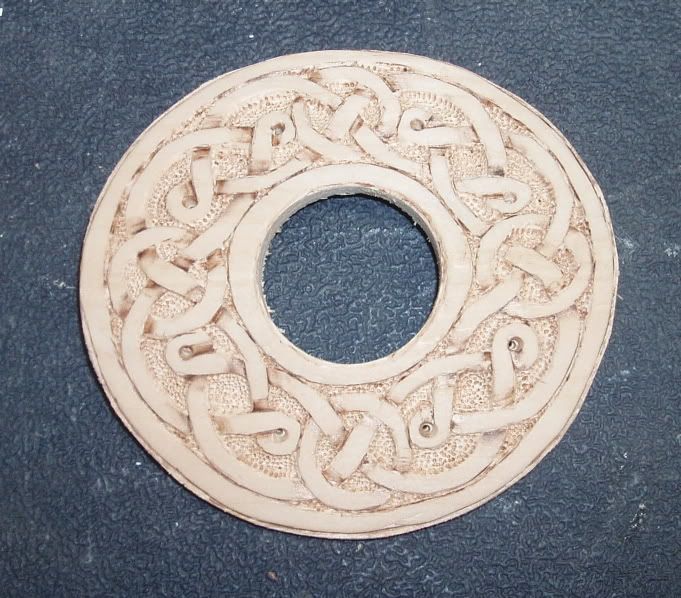
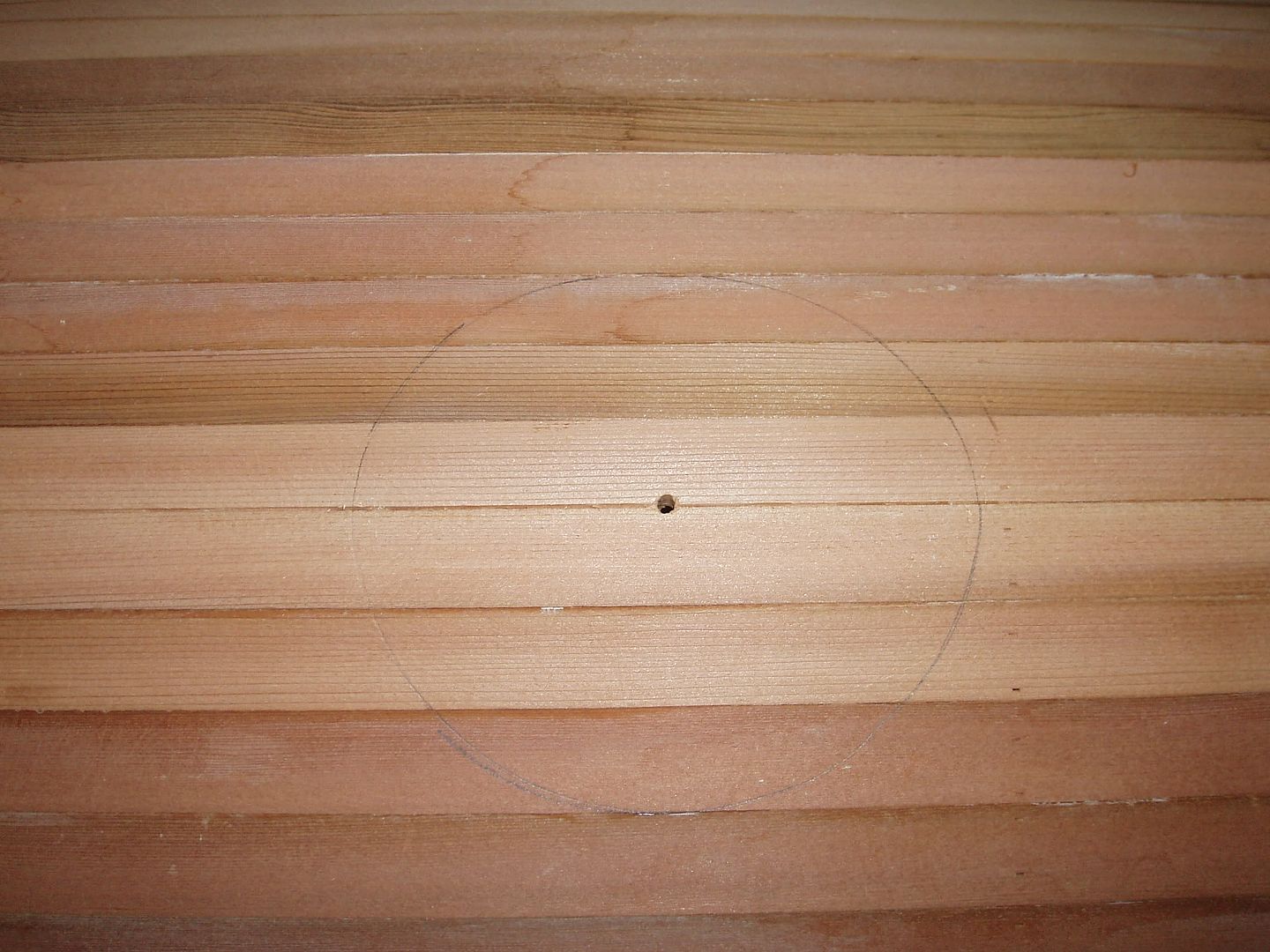
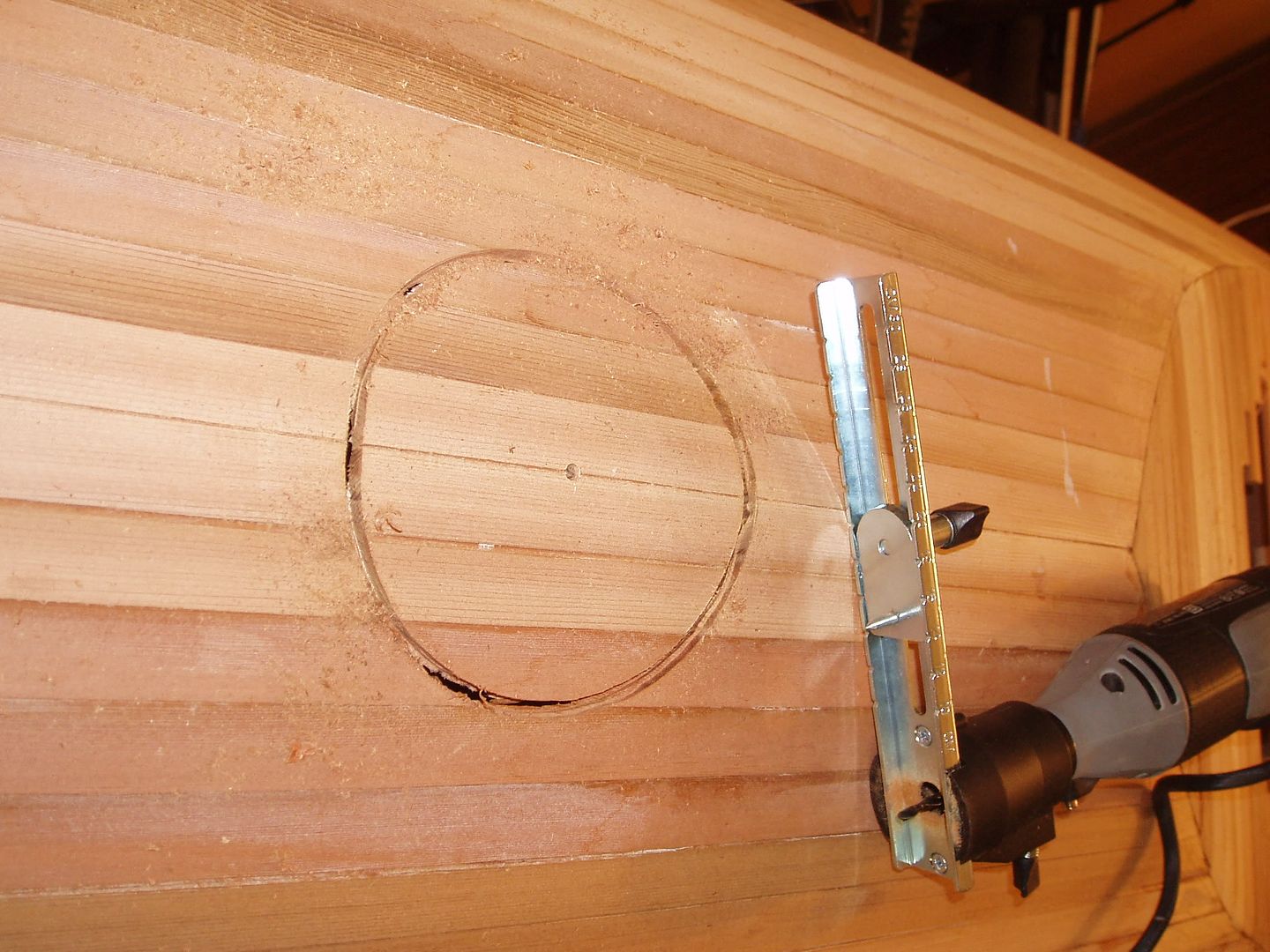
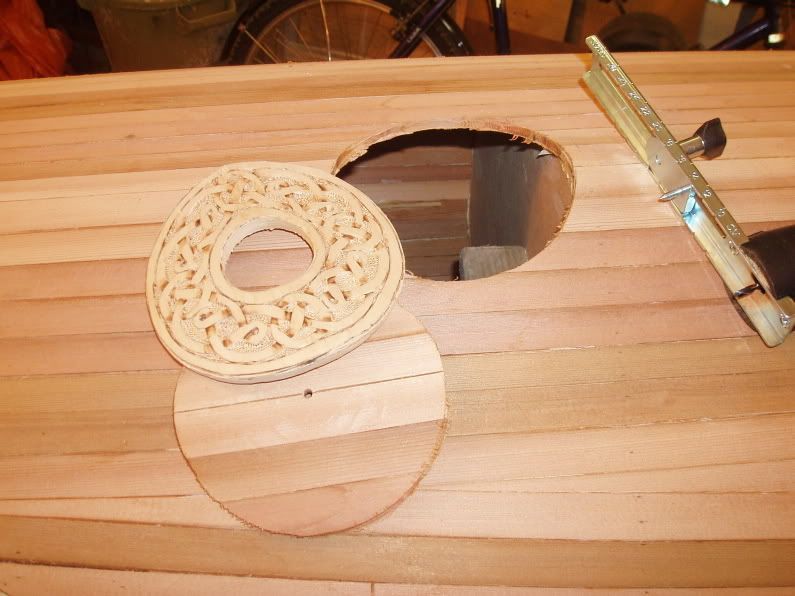
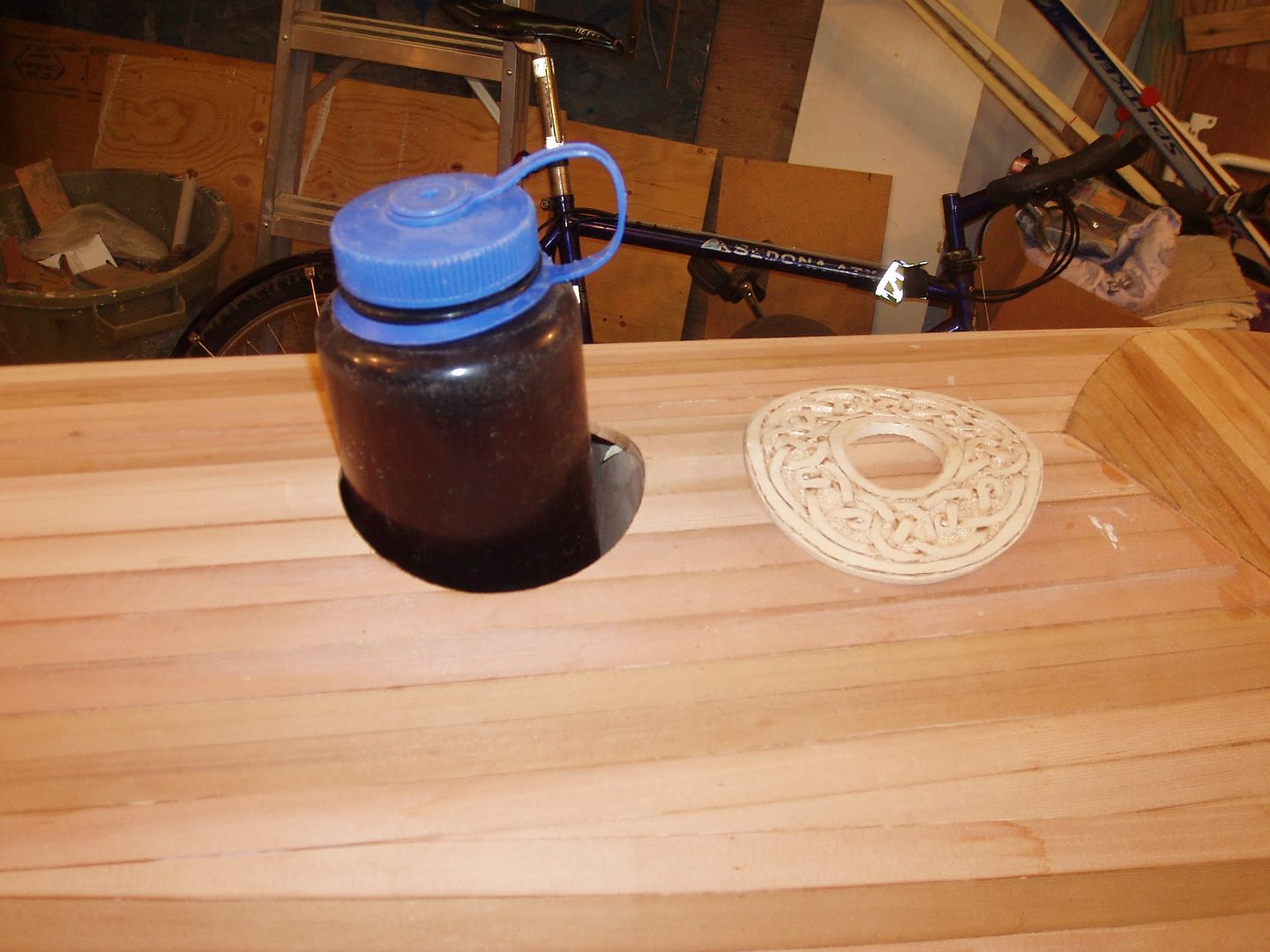
Initially, I was going to use a center disc of cedar cut from the deck but this proved not to work very well. Instead I used a piece of walnut to fill the center. Thin strips of walnut were also used to fill the gap around the outside of the carving as the hole in the deck was cut slightly oversize. This was done on purpose since the carved disc did not perfectly match the deck hole. If left as shown in the above photo, the imperfections would have been very obvious. Instead, I removed material in order to make a fairly even gap all the way around. As it is, it now looks like a design feature of a contrasting walnut border edging the carving, which goes well with the walnut center.
The carving was glued into place, supported from underneath by temporary supports (ie sticks) hot-glued to the underside of the deck. The edges were eased and the carving gently sanded along with the rest of the deck in preparation for fiberglass. The carving received a pre-coat of epoxy in order to fill in some of the relief of the carving and then was glassed along with the rest of the deck. During the fiberglass wet-out, some bubbles were still trapped in the relief but their effect was minor. Prior to the fiberglassing the underside of the deck, the bottom of the carving was planed & sanded flush with the rest of the deck. Two or three extra layers of 4 ounce glass cloth were applied to the underside of the carving and the immediate area just to strengthen & protect this spot. The end result was an inlaid carving that is slightly raised above the deck but cannot even be felt from underneath.
In the above photo, the carving along with the rest of the deck has been fiberglassed and the fiberglass sanded to a dull finish. The photos below were taken after another fill coat of epoxy was applied to the deck.
Finally, below is the finished product, dubbed the "engagement kayak."
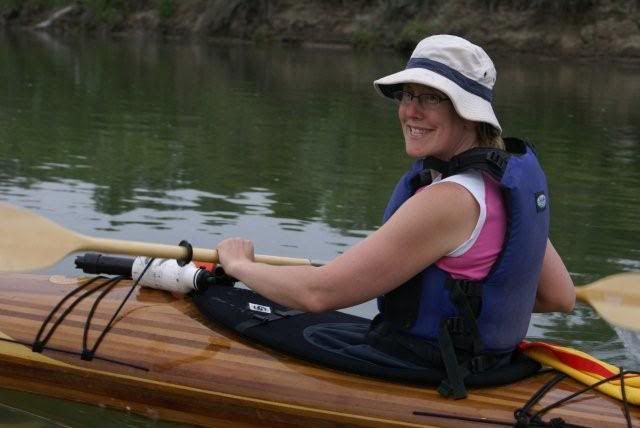
Tuesday, August 21, 2007
Facts & Figures
- Kayak Design: Guillemot
- Kayak Designer: Nick Schade
- Length: 17'
- Beam: 21"
- Waterline Length: 14.7'
- Build Start: October 2005 - setting up strongback and forms.
- First Strips On Forms: ~Nov 8, 2005.
- Point I Thought I Was Practically Done: June 29, 2006 after joining the deck and hull from the outside.
- Point I Realised I was Nowhere Near Done: December, 2006
- Completion: June 2007.
- Official Launch Date:June 16, 2007
- Total Time: 20 months with some interruptions.
- Woods Used: Western Red Cedar (hull & deck), Alaskan Yellow Cedar (bow of deck), Ash (stems), Walnut (accents on carved deck insert), Basswood (carved insert on deck), mahogany (hook for paddle park and inner stems), Pine dowel (grab loop holes), Birch plywood (bulkheads, cheek plates, coaming), unknown plywood that looks like mahogany (moby latches).
- Finished Weight: 42lbs fully fitted out, according to the bathroom scale.
- Amount of Epoxy Used: 1.5 gallons (approx.) West Systems
- Biggest Challenge: Taping inside seams then getting them smooth all the way to the stems after the epoxy had fully cured.
- Pleasant Surprise:Working with Alaskan Yellow cedar is very easy, and it smells nice too.
- Things To Do Differently Next Time:
- Build internal and external stems a la Ted Moores
- Move the front bulkhead aft at least 4" to increase hatch volume and decrease cockpit volume & wasted space.
- Mill my own strips, or ensure the quality of the milling.
- Don't use duct tape on the edges of the forms to keep the strips from sticking to the forms (it doesn't)
- Don't use the waxed masking paper to prevent epoxy from sticking where you don't want it to (it doesn't).
- Use fiberglass tape for the inside seam rather than strips cut from the regular cloth.
- Make the moby latches stronger, there's a surprising amount of force on them when they snap closed.
- Things I'd Do Again:
- Plywood coaming & riser. I wasn't sure the conventional method was best so I came up with a method using 1/8" birch ply that worked well for me.
- Create a design on the deck &/or the hull that breaks up the stripping a bit, reducing the number of finely tapered joints and making things easier in the long run.
- Carve an insert or inlay. I had never done it before and it turned out to be fairly easy & makes the boat totally unique.
- Use the internal strongback, mounted on an external strongback with wheels. Gives a secure and stable set-up. and creates a long narrow table which is a great place to keep tools handy.
- Atypical Features: Carved deck feature in the same pattern as our wedding bands, birch plywood coaming, "swoop" pattern of light wood across the bow & pin stripe down port side, moby hatch lid hold-downs, built on a "schade-style" internal strongback, supported on a "Moore's-style" external strongback.
- Tools Purchased For Kayak Building: Honing guide, glue bottle/spreader, saddle square, cornering tool, cabinet scrapers & case, carving knife, carving tool set, carver's saw (for cutting the cockpit hole, but a jigsaw with good blades worked better), fine cut jigsaw blades, rasp & blades (worked well), collapsible bottles for varnish, HEPA filter for shop vac (a very worthwhile purchase), latex gloves (turns out I might be allergic to latex now), many disposable brushes, radiant heater.
- Best Cheap Tool: A tie - the paint scraper and a $2 stamped metal small plane bought at a garage sale. Once sharpened properly, the paint scraper worked wonderfully for removing high spots, bumps, drips, runs, edges and excess glass/epoxy. The little hand plane just fits so nicely in the palm of my hand and it works very well for trimming strips and all sorts of other things while stripping. If I had lots of money, I'd upgrade to a Veritas apron plane. The microplane rasp gets an honourable mention.
- Tools To Buy Next: Better sharpening stones, dust collector with cyclone (but I probably won't). I'm sure I'll think of lots more when I start the next one.
- Money Spent: Not sure. About $1200 for wood, forms, fiberglass cloth, epoxy, varnish, glue, staples, cordage, etc. An uncertain amount went to electricity to heat the shop, tools, sandpaper, and other incidentals. Plus there was the paddle float, paddle, cradles for the roof rack, etc.
- People That Were a Big Help: Rob, Martin, my wife, Andy, Rod Tait (without whom I wouldn't have gotten the wood or the forms), Cory (my cousin that brought the lumber & forms from B.C. for me), and of course my daughters. Plus, everyone over at the Kayak Building Bulletin Board and the Bear Mountain Boats Forum for all the ideas, motivation, advice, feedback and problem solving.
Friday, August 17, 2007
Launched!
The photos below are all courtesy of Rick.

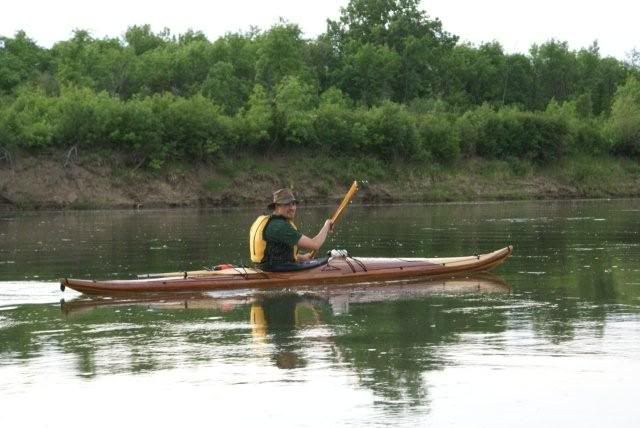
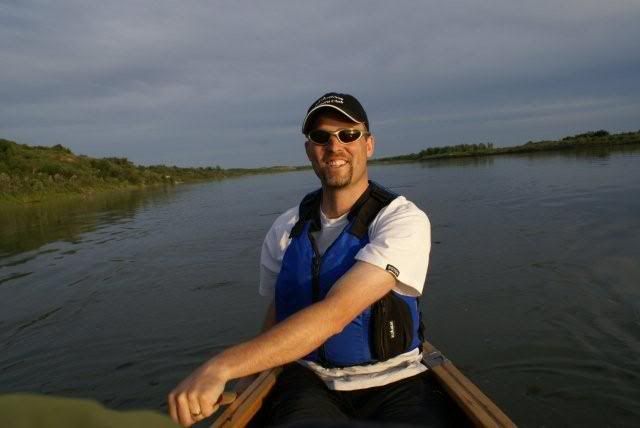
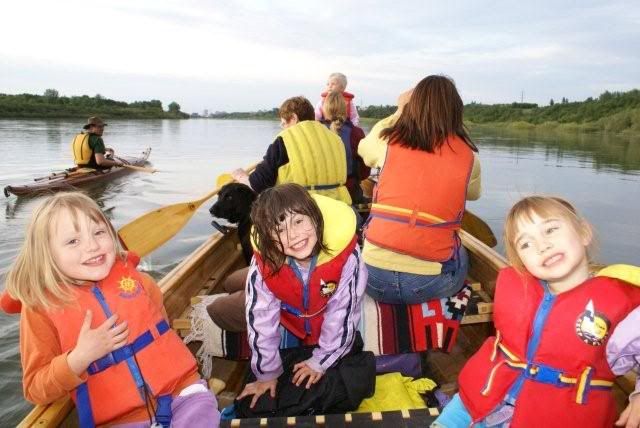
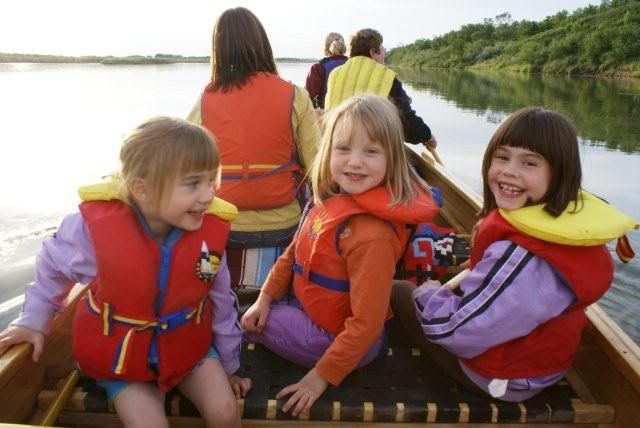

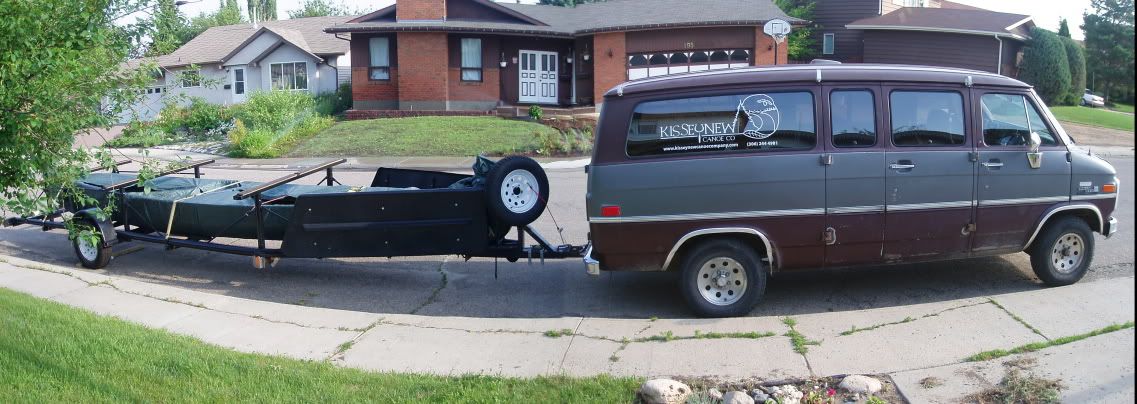
Tuesday, July 03, 2007
They Did it Again! And Again!!
This year, Martin wanted to do better. He built a new canoe this winter for the race, the "Precipice". The new canoe is 28' long, 36" wide (built to the limits of the rules allowed in the current YRQ rules) and looks like a rocket. It was stripped with 1/8" thick cedar strips, glassed on the outside with carbon fiber cloth and on the inside with kevlar cloth. Inside a couple of kevlar stringers were added to stiffen the lightweight hull. Fitted with seats & footrests, the completed canoe weighs 150 lbs (I think) which is pretty light for something of that size.
A team of 6 was assembled and has been training hard. The older 25' 10" canoe, the Sainte Anne, was used as well with a second team of 6 (the 2006 team was 8), called Kisseynew Skookum Asphalt.
This year, Kisseynew bettered their time by nearly 45 minutes with a finish of 42:16:47 in the Precipice. The competition was tough though and the 8-member team Coureur des Bayou finished about an hour ahead of Kisseynew at 41:15:00 for the first place finish, the first time a voyageur canoe has taken top honours in the YRQ. Third place overall, out of a field of 85 teams and 200 paddlers, was Kisseynew Skookum Asphalt with a time of 45:08:11. It appears that the Kisseynew has played a large part in changing the voyageur class of the YRQ from something of a novelty to a seriously competitive class as evidenced by the fact that the top 4 finishes in the 2007 race are all Voyageur canoes. This year the Kisseynew boats took home $1000 and $500 for second and third place, respectively. First place in the voyageur class received $2500, an improvement from 2006 as last year Kisseynew won $1500 for their first place finish in the voyageur class, $100 less than their entry fee! Ryan Martin of the Kisseynew Skookum Asphalt team was the first Yukoner across the finish line for the second year running.
By the way, there were at least 2 other wood boats in the race. Ken Brunton, a regular over at the Kayakforum.com trips forum was in the race but unfortunately scratched part-way through. Dave & Lisa McGee finished midfield in their cedar-canvas canoe.
Congratulations guys and hat's off to all who completed the race!
p.s. The kayak is completed and has been officially launched. However, I'm behind in posting. I'll get some photos of the completed boat and the launch up sometime soon.
Sunday, May 27, 2007
Torch River
Last weekend we went north to canoe on the Torch River. We drove up Saturday and met Larry in Choiceland and Larry led us towards the campground on the south side of the Torch River where we intended to launch that day. However, it seems that our Honda Accord (or perhaps my driving skills) were no match for the rural roads which are soft after the spring (a wet fall followed by heavy snows this winter), and made much worse by the couple of inches of snow they received the day before (odd feeling, driving in to a canoe trip passing fields completely covered in snow). We got stuck but thankfully Larry's son's 4x4 truck easily pulled us out. Extricated from the muck, Larry suggested that there may be another route, but we decided to play it safe and stick to the main roads, particularly since my mother-in-law was getting worried about having to shuttle our car on muddy roads. Thus, we launched from the Love bridge instead, and paddled to the White Fox bridge.
Though shorter than originally intended, our paddle Saturday afternoon was excellent. Our weather was cool with a breeze, but very warm in the sun. The high riverbanks were completely white with snow wherever there was shade. Areas that received a bit more sun were often yellow with flowers. The rapids along that stretch seemed larger and more numerous than I remember from last year. Since we were a lone canoe and travelling with our daughter in cool weather, we ran the river quite conservatively. That meant we didn't do as much "playing" as originally intended, passing by many opportunities to surf or practice eddy turns and focusing instead on having a dry run. It was funny to see our 5 year old daughter focused on snacks and quite oblivious to the whitewater while mom & dad negotiated a path amongst the boulders and rode through the waves. She had a lot of fun on the Torch and so did we. We had intended to run the river again Monday but in the end did not due to the steady rain which eroded away our resolve (and didn't improve road conditions either).